The project team improved upfront carbon outcomes through use of lower-strength concrete where feasible, limiting carbon-intensive materials, opting for carbon sequestering materials, reviewing EPDs, incorporating a significant number of salvaged materials, using high-recycled content materials, using structural materials as the final finish, and minimising waste.
In the design phase, the project adopted the mindset of “adaptive reuse and appropriate durability”. Given the retail typology, the project team focused on both the potential flexibility and disassembly of the base building, and guided tenants to undertake their fitout designs with regard to material/product selection, and accessible installation approaches to allow easier maintenance and deconstruction.
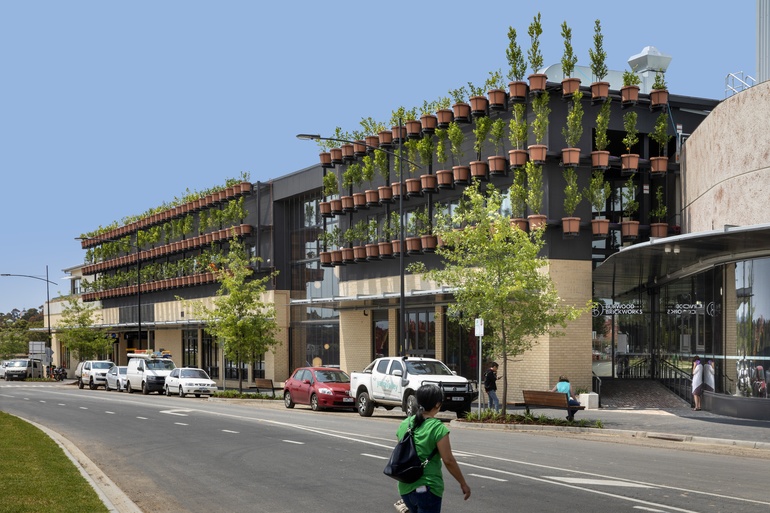
Additional systems and services were reduced in the first instance through passive design, e.g. maintaining daylight via the layout, and prioritising modular components across standard structural grids. High-traffic components were clearly designated from others and this differential wear and tear was considered in the design.
Clear spans in the supermarket, mall, cinema, and regularly spaced structural elements across the structural grid allow for multiple alternate uses of the interior in the future without costly structural alterations. Generous floor-to-floor heights are to be allowed throughout the mall and the tenancies on both levels, helpful for daylighting, natural ventilation, and adding or upgrading building services.
Flat floors with very few transitions from one floor height to another were ensured throughout, to allow more flexibility when renovating or change of use. Structural layouts across shopfronts allow flexibility across the interior openings, and intertenancy walls can be readily moved without heavily wasteful demolition.
Natural “honest” finishes were prioritised, which helped to avoid superfluous coatings that make items more bespoke and less likely to be salvageable in the future. In turn, these materials can better retain value, making them more feasible for reuse and recycling. In electrical items, plug-in devices were preferred over hardwiring to avoid re-engineering controls and entire systems for small future changes.
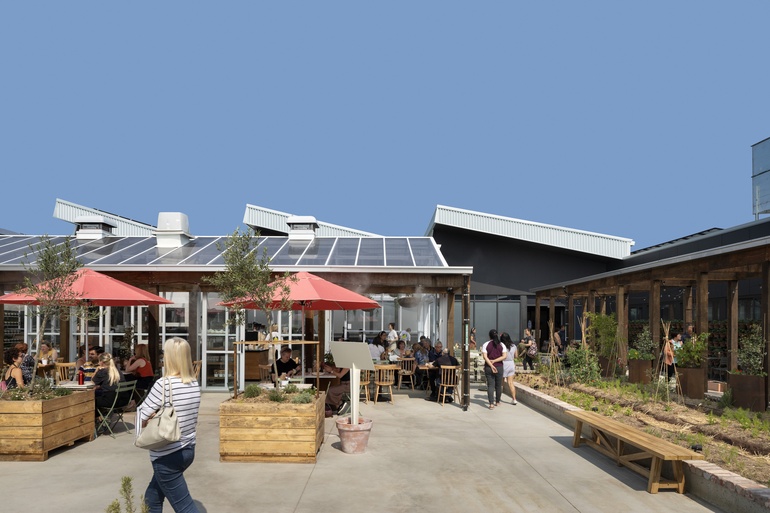
Through the construction phase of the project, the contractors had to commit to reducing environmental burdens from the extraction, processing, and disposal of materials. Subcontractors were encouraged to remove excessive packaging from products, where possible, prior to arrival on site.
Over-ordering was utilised as spare product were retained by the subcontractor for use on future projects. In the installation methodology repeatable mechanical (rather than toxic chemical) connections were made, which allows easier maintenance as well as deconstruction, and leaves labelling in place for easier reassembly in the components’ next life.
Considering the end-of-life phase, the project team focused on adaptability and deconstruction to allow for multiple alternate uses of the interior in the future designing flexible building services, whilst providing equity of access without costly structural alteration.